KI-optimiertes Laser-Remote-Schweißen
Die Zukunft von Large Language Models (LLMs) und künstlicher Intelligenz (KI) in der Optimierung von Laser-Remote-Schweißtechniken verspricht erhebliche Fortschritte in der industriellen Fertigung. Durch den Einsatz von KI-gestützten Technologien, wie sie von Unternehmen wie Trumpf und SiMa-ai entwickelt werden, können Lasersysteme effizienter und präziser arbeiten, indem sie Echtzeit-Datenanalysen zur Verbesserung der Prozessqualität nutzen und so die Produktionskosten senken und die Produktqualität steigern.
KI-gestützte Echtzeitüberwachung
KI-gestützte Echtzeitüberwachung ermöglicht eine präzise Qualitätskontrolle beim Laser-Remote-Schweißen. Moderne Systeme können mit Hilfe von KI-Algorithmen mehr als 3.000 Bilder pro Sekunde auswerten und kleinste Unregelmäßigkeiten im Schmelzbad, wie Poren oder Spritzer, zuverlässig erkennen. Diese Technologie nutzt multispektrale Sensoren und neuronale Netzwerke, um Fehler in Echtzeit zu identifizieren und zu klassifizieren, was zu einer deutlichen Steigerung der Zuverlässigkeit der Qualitätskontrolle auf bis zu 99,8% führt.
- KI-optimierte Sensorik ermöglicht die Echtzeitüberwachung des Laserschweißprozesses
- Neuronale Netzwerke werden an Millionen von Datensätzen trainiert, um robuste Fehlererkennung zu gewährleisten
- Integration von KI-Chips direkt in Lasersysteme beschleunigt die Datenverarbeitung und Prozessoptimierung
Deep Learning in Laserschweißen
Deep Learning-Technologien revolutionieren die Qualitätskontrolle und Prozessoptimierung beim Laserschweißen. Durch den Einsatz von Convolutional Neural Networks (CNNs) können komplexe Bildmerkmale aus IR-Aufnahmen des Schweißprozesses extrahiert und analysiert werden, was eine präzise Vorhersage von Parametern wie Fokuslage und Laserleistung ermöglicht1. Diese Methode erlaubt eine deutlich verbesserte Fehlererkennung und Prozessüberwachung im Vergleich zu herkömmlichen Ansätzen.
- Deep Learning-Modelle können mit über 98% Genauigkeit Poren und Splitter von weniger als 0,5 mm Größe detektieren
- KI-basierte Systeme ermöglichen die Erkennung von Nahtimperfektionen und Qualitätsabstufungen in Echtzeit
- Die Technologie ermöglicht es, bisher nur durch menschliches Erfahrungswissen erkennbare Muster in automatisierte Fertigungsprozesse zu implementieren
Edge-ML für Prozessoptimierung
Edge Machine Learning (Edge-ML) revolutioniert die Prozessoptimierung beim Laser-Remote-Schweißen durch die Verarbeitung von Daten direkt am Ort ihrer Entstehung. Diese Technologie ermöglicht eine zehnfache Steigerung der Leistungs- und Energieeffizienz bei ML-Anwendungen. Durch die Integration von KI-Chips direkt in die Lasersysteme können komplexe Berechnungen in Echtzeit durchgeführt werden, was zu einer deutlichen Beschleunigung der Materialbearbeitung führt.
- Edge-ML-Anwendungen ermöglichen eine effizientere Nutzung von Computer Vision bis hin zu generativer KI in Lasersystemen
- Die Technologie erlaubt die Auswertung von über 3.000 Bildern pro Sekunde zur Qualitätsüberwachung des Schweißprozesses
- Durch die Echtzeitanalyse können separate und aufwändige Prüfverfahren ersetzt und die Ausschussquote in der Produktion gesenkt werden
Sensorfusion für Echtzeitanalysen
Sensorfusion spielt eine entscheidende Rolle bei der Echtzeitanalyse von Laser-Remote-Schweißprozessen, indem sie verschiedene Sensordaten integriert, um ein umfassendes Bild des Schweißvorgangs zu erhalten. Diese Technologie kombiniert Daten aus optischen, akustischen und thermalen Sensoren, um die Qualität und Effizienz des Schweißprozesses zu verbessern.
- Optische Sensoren, wie Kameras und Fotodioden, ermöglichen die präzise Überwachung der Schweißnaht und helfen dabei, Abweichungen und Fehler in Echtzeit zu erkennen.
- Akustische Sensoren erfassen Schallwellen, die während des Schweißprozesses entstehen, was eine zusätzliche Dimension zur Fehlererkennung bietet.
- Thermale Sensoren messen die Temperaturverteilung im Schmelzbad, um sicherzustellen, dass die richtige Wärmemenge aufgebracht wird.
- Die Kombination dieser Sensordaten wird durch künstliche Intelligenz analysiert, um sofortige Anpassungen am Prozess vorzunehmen und so die Qualität der Schweißnähte zu optimieren.
Durch den Einsatz von Sensorfusion können Unternehmen die Genauigkeit und Effizienz ihrer Laserschweißprozesse erheblich steigern und so die Produktionsqualität verbessern.
Digitale Zwillinge
Digitale Zwillinge revolutionieren die Planung und Optimierung von Laser-Remote-Schweißprozessen. Diese virtuellen Abbildungen ermöglichen eine präzise Simulation des gesamten Schweißvorgangs, einschließlich der Anlagenkomponenten und des Werkstücks, mit einer Genauigkeit von bis zu ±2 mm. Durch den Einsatz digitaler Zwillinge können Techniker die Einrichtung und Kalibrierung von fahrerlosen Transportsystemen remote durchführen, was bei Großprojekten mit tausenden Stationen erhebliche Zeit- und Kostenersparnisse bedeutet.
- Digitale Zwillinge ermöglichen die virtuelle Erprobung verschiedener Schweißstrategien und Prozessparameter ohne physische Versuche.
- In der Chip-Herstellung werden umfangreiche physische Versuche durch Simulationen im digitalen Zwilling ersetzt, was die Entwicklungszeit und -kosten reduziert.
- Die Integration von Deep Learning-Algorithmen und KI in digitale Zwillinge schafft lernende und automatisierte Gesamtsysteme, die kontinuierlich optimiert werden können.
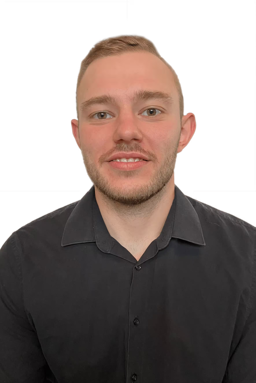
Matthias Mut
Experte in KI und Automatiserung. Spaß an Entwicklung, Fortschritt & Rapid Prototyping.